Today’s status quo
Wood-based panels or composite wood panels are products made from wood fibres, particles, strands or veneers, which are bonded together using adhesives. These panels are suitable for a wide range of applications in furniture making, building construction and interior design. The most common types are plywood, particleboard, OSB (oriented strand board) and MDF (medium density fiberboard).
A primary challenge for the adhesives used in wood-based panels manufacture is the dominance of fossil-based feedstocks, such as phenol, which are connected to various environmental concerns. There is a growing demand for sustainable, bio-based feedstock chemicals and materials to reduce the environmental impact of both adhesives and resultant wood-based products.
A further challenge for composite wood panels is the availability of wood feedstock at the required quality, quantity and cost. Although their production is based on sustainably managed forest resources, the expansion of the construction industry and the growing housing market trends lay pressure on the ever-limiting wood reserves. Alternative raw materials and recycling options are in the spotlight of current industrial research to overcome the limited wood availability and to reduce the environmental impact of wood-based panels.
DigInTraCE innovation routes
The project addresses the above-described challenges by developing two solutions:
- bio-based adhesives for plywood production, derived from plant proteins
- particleboards produced from secondary wood
DigInTraCE participant CHIMAR uses protein recovered from sunflower and rapeseed press cakes to substitute petrochemical phenol in typical phenol-formaldehyde (PF) resins, to the highest possible level. The properties of the thus synthesized bio-based resins are evaluated against those of reference resins and their adhesion performance is tested and qualified through the production of plywood type panels at the pilot facility of CHIMAR. Partner NTUA undertakes the extraction of protein from oilseed crop processing residues (press cakes) to supply CHIMAR with the needed protein feedstock.
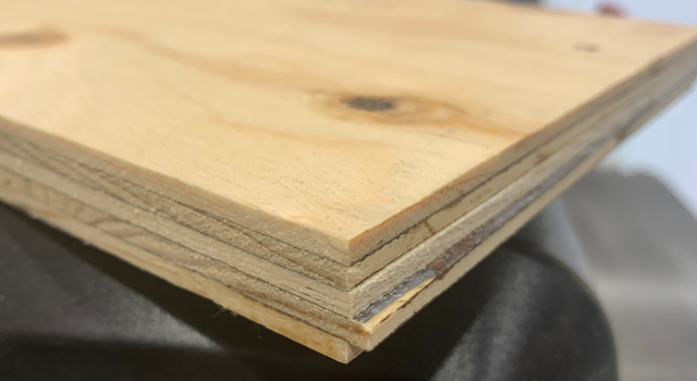
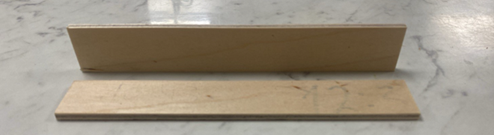
Pictures 1-2: Plywood produced with protein-based phenolic type resin at the pilot facility of CHIMAR.
A further route followed by CHIMAR is the pilot production of particleboards using mixtures of fresh and secondary wood chips, recovered from wood by-products, and conventional urea-formaldehyde type resin as the binding adhesive. The secondary wood chips are derived by the mechanical disintegration of wood residues from furniture manufacturing at partner MENEXES. Wood residues till now used for heat generation, such as uncoated panels (particleboards, OSB, solid wood parts and the like) are collected by MENEXES, characterized and mechanically degraded by CHIMAR, and sorted by ICCS, DigInTraCE coordinator. The secondary wood chips thus obtained are applied in particleboard production at CHIMAR pilot unit replacing partly the fresh wood chips used. Through subsequent testing, the performance of the produced particleboards is compared to that of reference panels, aiming to achieve equivalent or even superior panel properties.
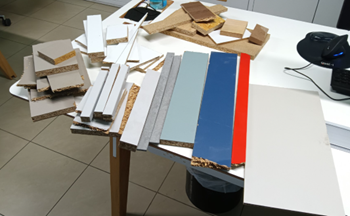
Picture 3: Wood residues from furniture manufacturing at MENEXES.
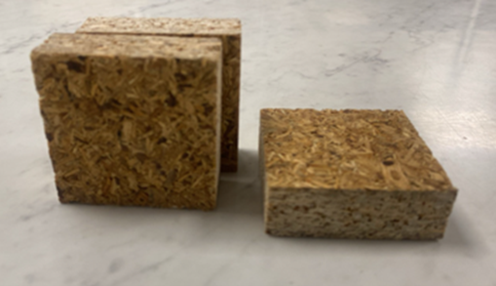
Picture 4: Particleboard made from 15% recycled chips.
Towards a sustainable future
DigInTraCE project embodies the principles of the circular economy not only by promoting the efficient utilization of organic residues and wood by-products, but also by creating innovative and sustainable value chains and products (e.g. bio-based adhesives, panels from secondary wood) with reduced environmental impact. In a time when protecting the future quality of life on earth is needed more than ever, DigInTraCE solutions may prove of high value.
This blog post was created by CHIMAR partners: Dimitrios Moutousidis (MChemEng), Eleftheria Athanasiadou (MChemEng, MBA), Dimitrios Argyropoulos (MChemEng, MBA).